Eur Ing David Boettcher CEng MIET FBHI
In the article about my grandparents’ watches in the previous issue of TimePiece, I mentioned that my grandfather’s watch has a white alloy balance spring that is most likely a nickel steel alloy of the type invented by Paul Perret and Dr Guillaume in 1897. The invention of nickel steel balance springs was a major development in watchmaking; this article briefly explains how it came about.
A watch’s rate is determined by the frequency of oscillation of its balance, which is principally determined by the rotational inertia of the balance and the stiffness of the balance spring. The effects of changes in temperature on the balance and spring were a problem for early watchmakers. As temperature rises, thermal expansion of the balance increases its rotational inertia, slowing the watch. At the same time, a steel balance spring’s modulus of elasticity reduces, lessening its stiffness, which also slows the rate. The balance spring also expands. Increases in length and height nullify each other, but its increase in thickness makes the spring stiffer, which, on its own, would cause a gain. Due to these effects, a watch with a steel balance spring and plain brass balance loses about 11 seconds per day for each degree Celsius temperature rise.
John Harrison’s invention of the bimetallic strip, ultimately resulting in the compensation balance, enabled the effects of temperature to be compensated, but compensation balances were expensive to make and adjust and delicate to handle.
In the 1890s, Dr Charles Édouard Guillaume worked at the International Bureau of Weights and Measures in Sevres, a suburb of Paris. A length standard made of nickel steel sent to the bureau by the artillery section of the French army for calibration was found to have a rate of thermal expansion significantly different from that predicted by the rule of mixtures from its proportions of iron and nickel, which attracted Guillaume’s attention. Other samples of nickel steel subsequently sent to the Bureau were also found to have unexpected thermal expansion rates. Following these observations, Guillaume made a systematic study of the rates of thermal expansions of a wide range of nickel steel alloys with the assistance of the Société de Commentry-Fourchambault & Decazeville, the steelworks at Imphy in Burgundy that made the nickel steel alloys. One result of this investigation was the discovery of Invar, a nickel steel alloy with 36% nickel and a very low thermal expansion rate.
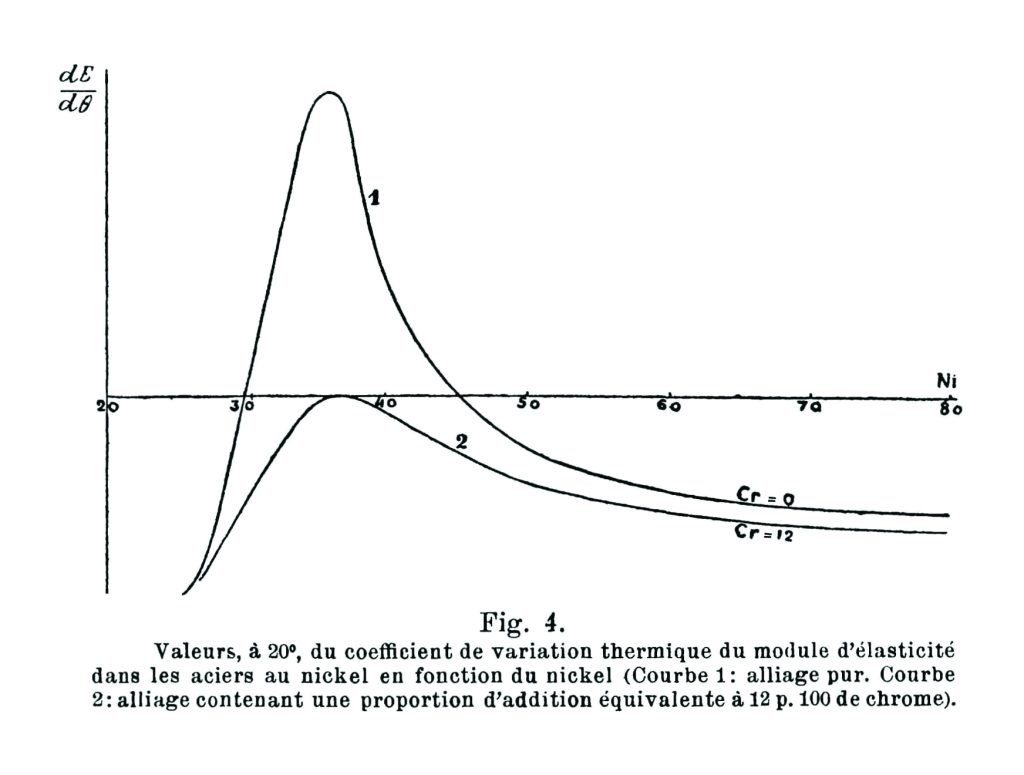
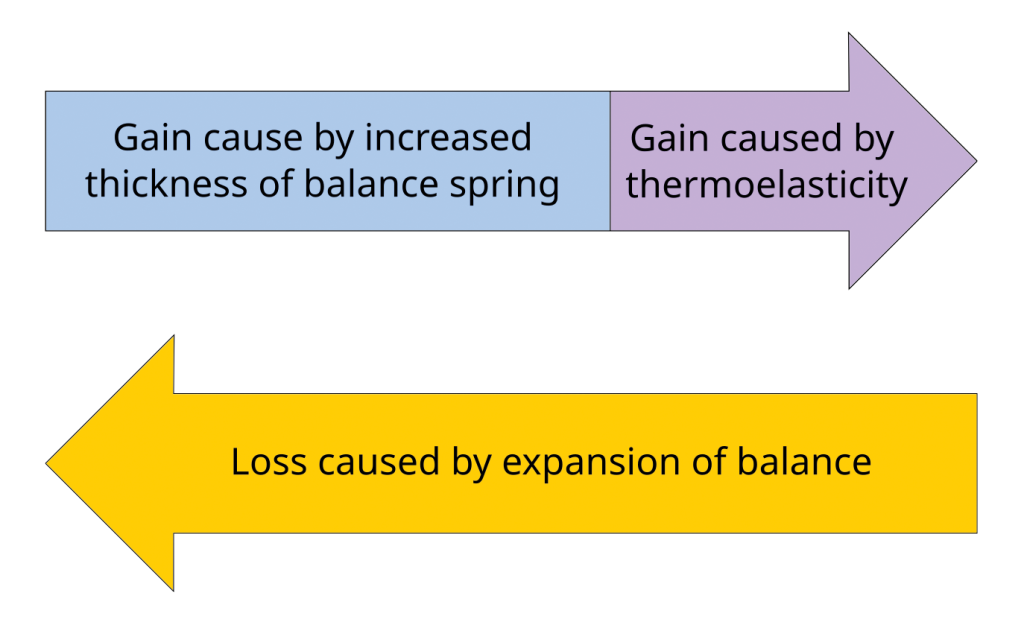
After presenting his findings to the French Academy of Science in the spring of 1897, Guillaume received a letter from Paul Perret, a watch springer and timer in La Chaux-de-Fonds,
requesting a sample of Invar. Guillaume, having a spare piece of Invar wire, obliged. Two weeks later, Perret wrote again, requesting samples of all the other nickel steel alloys that Guillaume had studied. However, this time, Guillaume refused. A few days later, Perret arrived unexpectedly at Guillaume’s office in Sevres.
Guillaume recounted their meeting: Paul Perret said: ‘With the Invar specimen you sent me, I made balance springs and found results that astonished me.’
I said: ‘I know.’
Paul Perret (no doubt surprised by this reply) asked: ‘How do you know?’
I said: ‘If you had not found extraordinary results, you would not be here in Sèvres.’
Paul Perret replied: ‘That’s true!’
It’s not difficult to imagine an outbreak of mutual smiles or laughter.
Perret had discovered that a watch fitted with a balance spring made from the sample of Invar gained significantly when its temperature was increased, precisely the opposite of a watch with a steel balance spring.
This discovery revealed that Invar has a positive thermoelastic effect, which means that its modulus of elasticity increases as it is heated. This is extremely unusual. Since the discovery of Invar, positive thermoelastic effects have been observed in a few materials, but the effect is uncommon; almost every metal alloy becomes less stiff when heated. A cantilever beam made of steel with a weight suspended from its free end bends further when heated, lowering the weight. A similar beam made of Invar straightens when heated, raising the weight.
Whilst a watch with a steel balance spring and plain brass balance loses about 11 seconds per day for each degree Celsius increase in temperature, mainly due to a reduction in the balance spring’s elastic modulus, the watch that Perret fitted with an Invar balance spring gained 18 seconds per day for each degree Celsius. This was so unexpected that Perret told Guillaume he thought he might have gone mad!
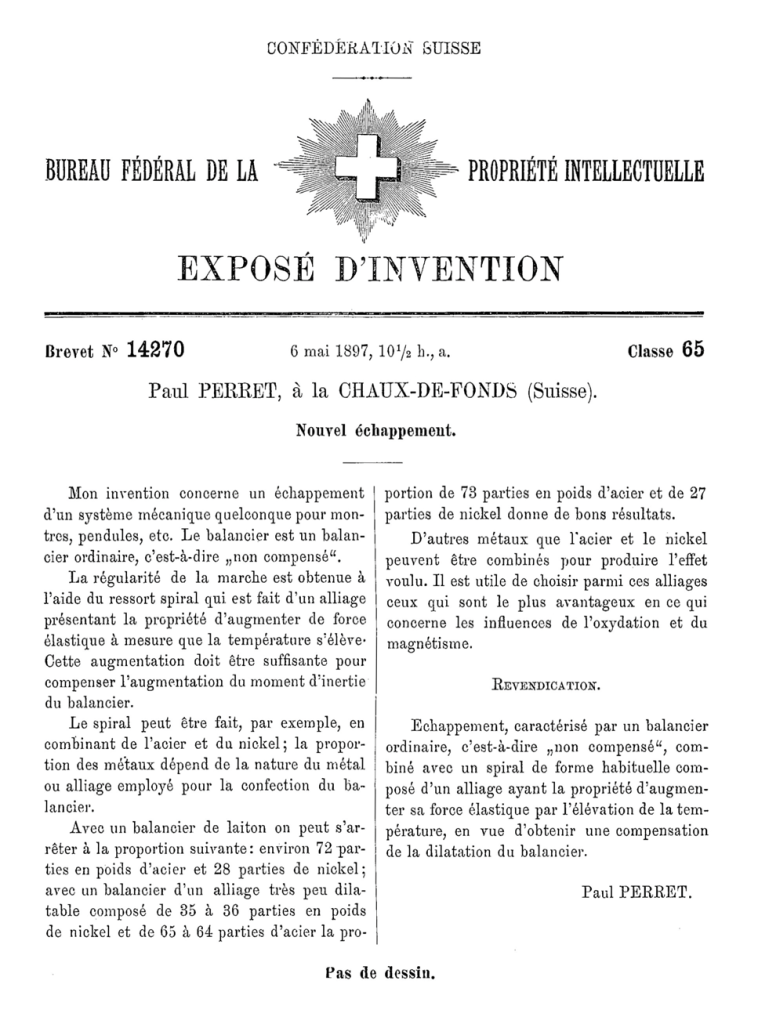
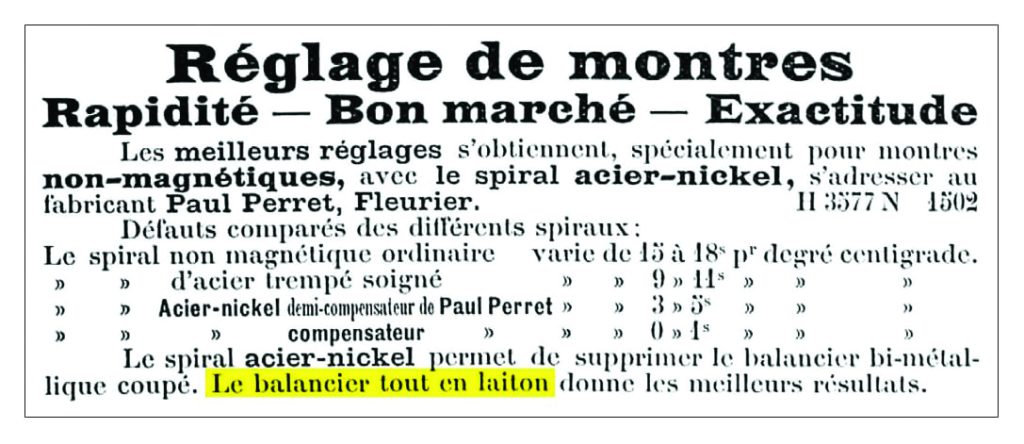
Knowing that a watch with a steel balance spring loses about 11 seconds per day per degree and having discovered that a watch with an Invar spring gains about 18 seconds per day per degree, Perret reasoned that somewhere between steel and Invar, there should be a nickel steel alloy that would cause no variation in rate with temperature changes.
He explained this to Guillaume, and they agreed to collaborate. At the time, the best way to determine the thermoelastic effect of an alloy was to make it into a balance spring, fit this to a watch and record the rate at different temperatures, from which the thermoelastic coefficient of the spring material can be calculated. Perret and Guillaume worked together in the summer of 1897 to measure the thermoelastic effects of different nickel steel alloys in this way. The results are plotted as curve 1 in the figure reproduced as Figure 1. This shows the thermoelastic coefficients on the y-axis plotted against increasing nickel concentrations on the
x-axis. Curve 1 peaks in the positive region at around 36% nickel, corresponding to Invar, which caused the result that astonished Perret. It crosses the zero x-axis between 27% and 28% nickel and between 43% and 44% nickel. At these two points, the elastic modulus does not vary with temperature changes, another very unusual property.
On 6 May 1897, Perret applied for a Swiss patent on his idea, which was granted Swiss patent number 14270, Figure 2. It only remained to put the idea into practice. Subsequently, Guillaume recorded that on 20 August 1897, in Perret’s workshop in La Chaux-de-Fonds, he witnessed a watch with a plain, that is not compensated, balance and a nickel steel balance spring that ran at the same rate at temperatures of zero and 30 degrees Celsius. An uncompensated watch with a steel balance spring would run 330 seconds, or five and a half minutes, slower, so this was a significant breakthrough.
Invariable Elasticity?
It should be noted that the balance spring of the watch witnessed by Guillaume in Perret’s workshop did not have invariable elasticity.
It is sometimes thought that combining a balance spring of invariable elasticity and a balance with a low thermal expansion would form an oscillator unaffected by changes in temperature, but that is not the case. It doesn’t work because the stiffness of a spring is not determined solely by the elastic modulus of the material from which it is made. The elastic modulus, or Young’s modulus, is a property that is independent of dimensions. A thicker spring is stiffer than a thinner one. A spring’s stiffness depends on its elastic modulus and dimensions. A material with invariable elasticity does not make a spring of invariable stiffness; thermal expansion makes the spring stiffer even if its modulus of elasticity does not alter.
Guillaume summarised the problem and its solution very succinctly:
‘In practice, what one should look for is not an alloy whose thermoelastic coefficient is strictly zero, but an alloy such that the thermal expansion of the balance and the spring, and the thermoelastic variations of the latter, give a zero sum.’
Perret’s patent described two possible embodiments of this idea. The first features a balance spring made from an alloy of 28% nickel and 72% steel with a brass balance. The second uses a balance spring of 27% nickel and 73% steel with an Invar balance.
In both cases, the spring’s combination of thermoelasticity and thermal expansion causes it to become sufficiently stiffer with increasing temperature to compensate for the balance’s thermal expansion. To achieve this, the two nickel steel alloys Perret
defined fall on either side of the point of zero thermoelastic effect between 27% and 28% nickel.
The alloy with 28% nickel is in the region where the thermoelastic effect is positive. This effect, along with thermal expansion, increases the spring’s stiffness to compensate for the expansion of a brass balance.
The thermal expansion of an Invar balance is much less than that of a brass balance; thermal expansion of the spring causes a greater increase in stiffness than is necessary to compensate for this, which would result in a residual gain. The alloy with 27% nickel is in the region with a negative thermoelastic effect, reducing the modulus of elasticity to compensate for the excess increase in stiffness. However, Perret dismissed the idea of an Invar balance, saying that it presents no advantage and has the disadvantage of being magnetic and very difficult to work with. Invar balances have never been used in watches.
Figure 3 shows the effects of thermal expansion and thermoelastic changes following a temperature increase of 30 degrees Celsius on the rate of a watch fitted with a 28% nickel steel balance spring and brass balance. Expansion of the balance would cause a loss of 48 seconds per day, but the gains of 29 seconds caused by expansion of the balance spring and 19 seconds caused by the thermoelastic effect compensate for this, resulting in an overall zero rate.
The first nickel steel balance springs were sold under the name of Paul Perret. Figure 4 is an advert for Paul Perret nickel steel balance springs from 1901. The statement at the bottom says that nickel steel balance springs make cut bimetallic balances, that is, compensation balances, unnecessary and that a balance made entirely of brass (‘tout en laiton’) gives the best results.
These first nickel steel balance springs were soft and had high internal friction. They also had a significant secondary error because their thermoelastic coefficients were not constant over a range of temperatures, making them unsuitable for the highest-quality watches. They were used to provide temperature compensation for millions of cheaper watches, which did not justify the cost of a compensation balance. Many of these have not survived because of accidental damage to the balance spring during servicing due to the delicate nature of the spring. An
English company that used Paul Perret balance springs was H. Williamson of Coventry. Figure 5 shows one of their adverts from 1910, and Figure 6 shows the balance and spring of one of their watches from around that time – a rare survivor.
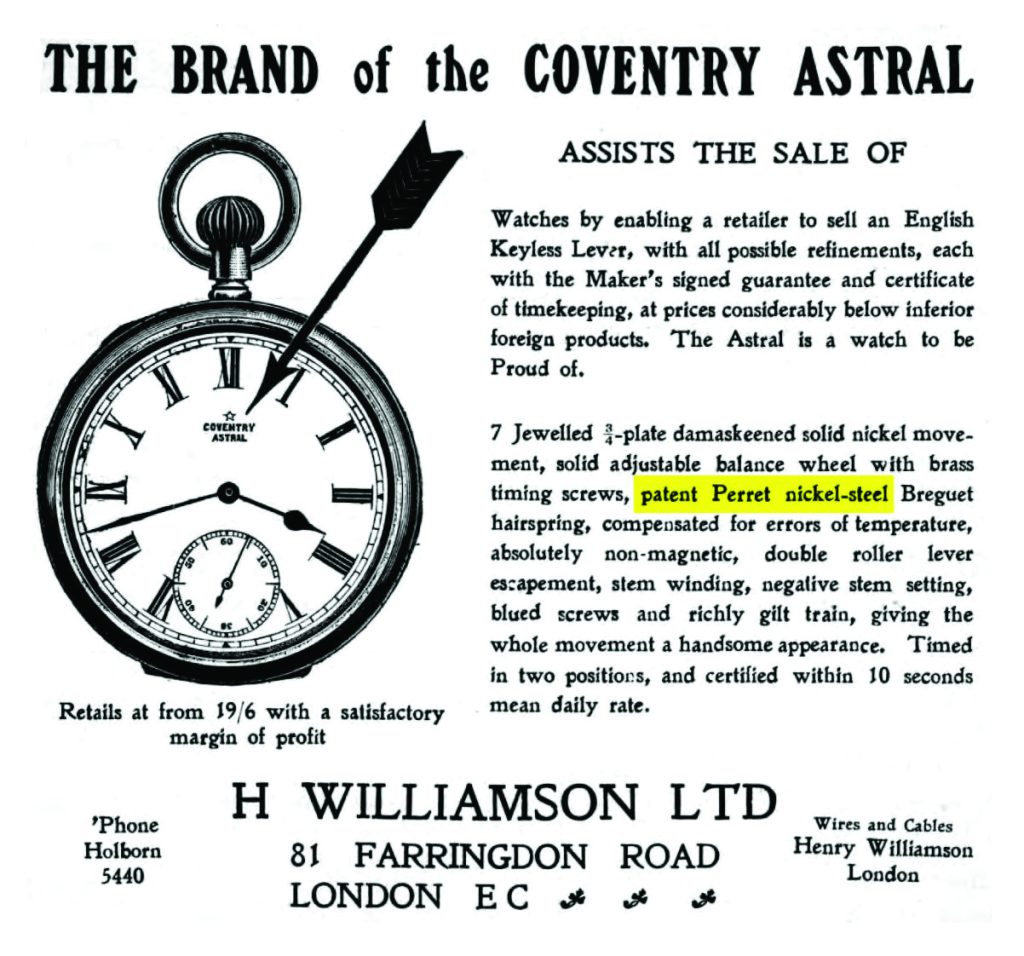
Spiraux compensateurs du Dr Guillaume
To improve the properties of nickel steel balance springs, small amounts of solution-hardening elements, including chromium, carbon, tungsten, manganese, silicon, molybdenum, vanadium, tantalum, and titanium, each in a proportion between 0.2 and
4 percent, were added to make an alloy that had a higher elastic limit and lower internal friction while retaining the same temperature-compensating properties.
Dr Guillaume and the Société des Fabriques de Spiraux Réunies applied for two patents for this invention on 20 February 1911, and they were granted Swiss patent numbers 54715 and 54876. The two patents had similar titles, referring to an alloy with an elastic force increasing with temperature and a high elastic limit. Two corresponding British patents, numbers 3846 and 3847, were subsequently granted in 1912 for this invention, and two United States patents were granted in 1914.
In the Swiss patents, the term ‘elastic force’ was used instead of stiffness. The ‘elastic force’ generated by any balance spring varies from zero at the neutral position to a maximum at the
extremes of the balance’s motion on every cycle; the spring’s
stiffness must increase with rising temperature to compensate for the increasing inertia of the balance. The body of the patent correctly explains that it is the modulus of elasticity that increases with temperature. In the British patents, it is said that the ‘elasticity’ of the spring increases with temperature, which is decidedly wrong. Elasticity, or elastic compliance, is the reciprocal of the elastic modulus. Balance springs made from this alloy were sold as ‘Spiraux compensateurs du Dr Guillaume.’
Elinvar
The Imphy Steelworks recruited the metallurgist Pierre Chevenard to set up a new, state-of-the-art metallurgical laboratory. He discovered that nickel steel would accept a much greater amount of chromium as an alloying element than had been thought possible. A nickel steel alloy with 12% chromium was found to have much greater hardness, lower internal friction, and better thermoelastic characteristics. This is shown as curve 2 in Figure 1.
It is well known that Guillaume coined the name ‘Elinvar’ for this alloy from ‘invariable elasticity’. However, Elinvar is a very misleading name, and the intersection of curve 2 with the zero
x-axis is not drawn accurately for a balance spring material. Elinvar balance springs have a much lower thermoelastic coefficient than steel, but it is not zero as shown. They have a positive thermoelastic coefficient and an elastic modulus that
increases with temperature, just like the Paul Perret and Guillaume balance springs that preceded them. Elinvar also expands when heated; Guillaume stated that the rate of thermal expansion of Elinvar is 8×10-6 per degree Celsius, which is about three-quarters that of steel.
The new alloy was discovered in 1913, but the Imphy steelworks could not produce it commercially before the war broke out in 1914. After that, the French army needed all the nickel steel produced by Imphy. Consequently, Elinvar balance springs were not manufactured until after the war.
Because perfectly mixing the alloying elements is difficult, Elinvar balance springs have a range of thermoelastic coefficients. To achieve the best possible rates, Paul Ditisheim invented the Affix balance, with small bimetallic affixes that were used to tune the balance’s thermal expansion rate to match the characteristics of a particular spring.
Another type of balance with an adjustable expansion rate is the ovalising balance, invented by Paul Perret in 1897. These increase their mean radius and rotational inertia with increasing temperature, the rate of which can be adjusted by moving screws around the rim. Hamilton used ovalising balances in their Model 21 marine chronometer, with their own balance spring material called Elinvar-Extra, which, like the Paul Perret nickel steel alloy and Elinvar, has a positive thermoelastic effect.
Nivarox
In the 1920s, Reinhard Straumann heard of the use of beryllium to harden copper by precipitation hardening. Precipitation hardening differs from the solution hardening used for Elinvar and similar alloys. When quenched from a high temperature, at which the elements are fully soluble, the alloy is soft and easy to form; its strength is developed by heating it to the lower precipitation temperature at which precipitates form and impede dislocation movement.
Straumann wondered if Elinvar could be hardened by adding beryllium. Beryllium has a high affinity for oxygen and would form oxides in an open crucible such as used at the Imphy
steelworks, so Straumann contacted Heraeus Vacuumschmelze of Hanau, who had pioneered vacuum induction melting so that alloys could be made under a vacuum. It was necessary to add additional alloying elements to maintain the required thermoelastic coefficient, but the work was eventually successful, and an application for a patent was submitted in April 1931.
Straumann called the new alloy Nivarox, from the German ‘nicht variable, nicht oxidierend’ (non-variable, non-oxidising). Nivarox has properties comparable to hardened and tempered carbon steel springs but retains the thermal compensation characteristics of nickel steel alloys discovered by Paul Perret and Dr Guillaume.
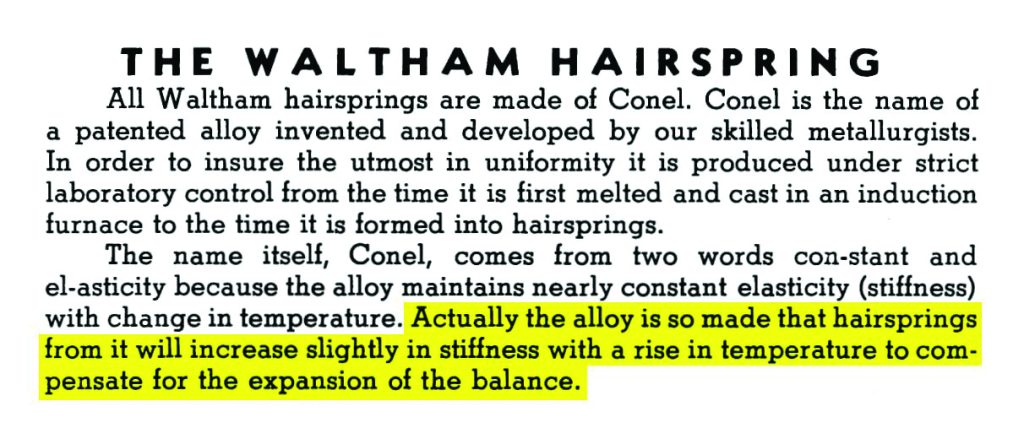
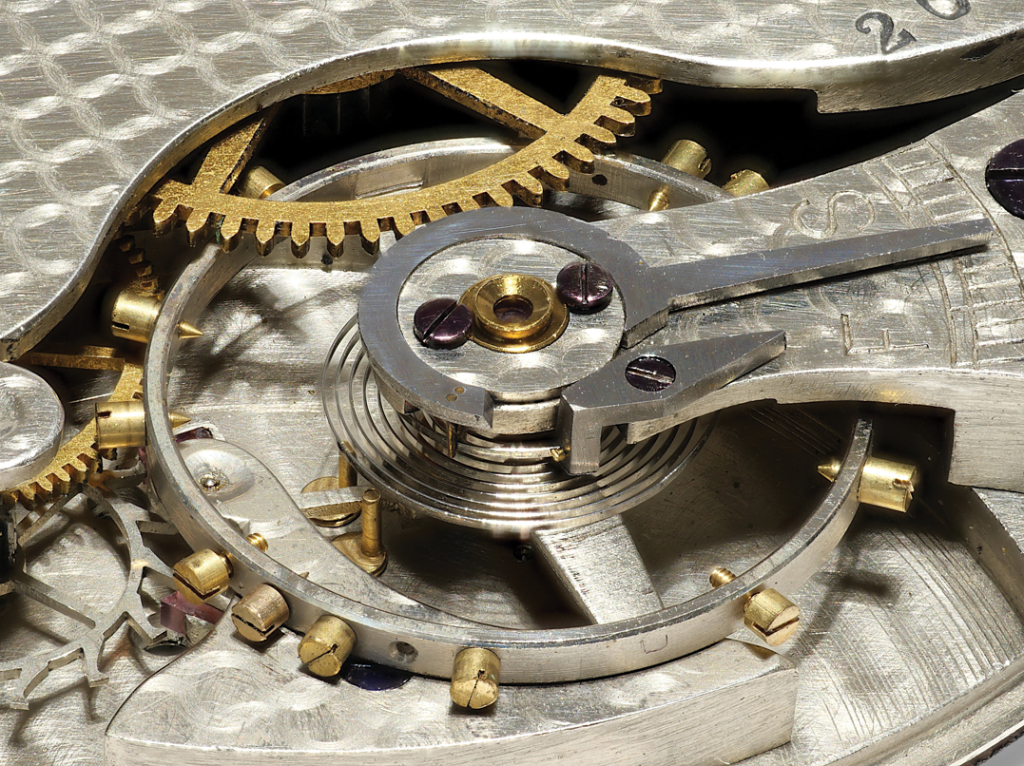
Balances
The plain, uncut balances used with nickel steel balance springs are described as ‘monometallic’ to distinguish them from bimetallic compensation balances. Brass balances were
superseded by Maillechort, an alloy of copper with zinc and nickel that is non-magnetic, oxidation-resistant and harder than brass, although having the same thermal expansion rate. In
English, this is called nickel silver from its appearance, although it contains no silver.
Maillechort was superseded by Glucydur, a beryllium copper alloy named after glucinium, an old name for beryllium, also called CuBe, after the atomic symbols of copper and beryllium. The amount of beryllium in the alloy is small, only a few percent. Hence, the material is principally copper, and its coefficient of thermal expansion would, therefore, be expected to be essentially the same as copper, which is not small. However, Glucydur is sometimes described as having a low thermal expansion; Swatch Group were asked about this. They stated that Glucydur is an alloy of copper with 2% beryllium and a coefficient of thermal expansion of 17×10-6 /°C, which is about the same as brass.
Textbook Treatment
This subject is not well treated in English language textbooks. In The Science of Clocks & Watches, Rawlings says that Dr Guillaume ‘produced Elinvar, an alloy with invariable
elasticity.’ This shows a fundamental misunderstanding of temperature compensation using nickel steel alloys. Only in his description of Waltham’s Conel alloy does he get the explanation correct, saying that Conel alloy ‘is so adjusted that the change of its elasticity (including that due to its expansion) compensates for the expansion of the balance.’ He is probably quoting from publicity material such as the Waltham Watchmaker’s Handbook, shown in Figure 7. Conel was another unfortunate choice, implying that the elasticity doesn’t change. A note added after explaining the word’s derivation clarifies the situation; if only Elinvar had such an explanation attached.
Richard Good, in the 16th edition of Britten’s Handbook, correctly describes Elinvar, Nivarox and similar types of balance springs as ‘low thermoelastic coefficient springs’, but he goes on to say that Ditisheim’s Affix balances were created to compensate for springs with ‘either an excessively positive or negative thermoelastic coefficient.’ This is wrong. All Elinar balance springs have positive thermoelastic coefficients. Ditisheim’s Affixes were created so that the thermal expansion rate of a balance could be matched to the characteristics of a particular Elinvar balance spring. It is surprising that two such well-known textbooks, written many years after Paul Perret and Dr Guillaume invented temperature-compensating nickel steel balance springs in the late nineteenth century and subsequent developments over the next 40 years, including Elinvar and Nivarox, contain so little on the subject. What they do contain shows a fundamental lack of
understanding.
Misleading Names
The name Elinvar often leads people to erroneous assumptions. Knowing that it is derived from Élasticité invariable or invariable elasticity, they assume that a balance spring made from it will not change stiffness with temperature changes. But in choosing the name Elinvar, Guillaume meant only that the modulus of elasticity was invariable, not that a spring made from it would have invariable stiffness; he knew perfectly well that Elinvar expands when it is heated, which causes a spring to increase in stiffness.
Guillaume was a scientist, a metrologist, and not a professional horologist, which may have influenced his thinking. For many applications, Elinvar can be regarded as having a modulus of
elasticity that does not alter significantly with temperature changes, and after the fame he had gained from his earlier discovery being named Invar, another similar, catchy name would have been very tempting, even if it was not strictly accurate. But watches are very sensitive to changes in the stiffness of their balance springs, and Elinvar cannot have invariable elasticity when it is used for a watch balance spring, just as Invar cannot be taken as having zero thermal expansion when it is used as a pendulum rod.
Guillaume must have known that nickel steel balance springs could not be made with invariable elasticity. Swiss patent 54876 of 1911 begins, ‘It is known that for several years, escapements have been constructed with balance springs whose elastic force increases with temperature, which largely compensate for the increase in the inertia of the balance with the temperature rise. It is, therefore, strange that in some articles, Guillaume stated that Elinvar has invariable elasticity. However, in a paper about Elinvar presented to the French Academy of Sciences in July 1920, he added the following explanatory remark…
It should be noted, in fact, that the indication … of a zero value of the thermoelastic coefficient was intended, above all, to simplify the presentation. What we must look for in reality is an alloy endowed with a thermoelastic coefficient with very low linear variation and of a value such that its action, associated with the sum of the effects of expansion, acting in the opposite direction, of the balance spring and balance, leads to the perfect equalisation of the rate of chronometers throughout the temperature range of their use.
So that’s it. Guillaume’s description of Elinvar as having a zero thermoelastic coefficient and deriving its name from invariable elasticity was intended to simplify things. Instead, it has caused more than a century of confusion.
Final Thoughts
A spring’s stiffness depends on its elastic modulus and dimensions. A material with invariable elasticity does not make a spring of invariable stiffness; thermal expansion makes the spring stiffer even if its modulus of elasticity does not alter.
Watches with monometallic balances do not achieve temperature compensation by using a balance spring with invariable elasticity and a balance with a low thermal expansion. Instead, they use a balance spring whose combined thermal expansion and thermoelastic variation compensate for the balance’s thermal expansion.